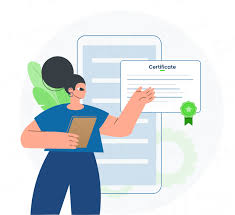
Industries in India that handle compressed gases, petroleum, explosives, and hazardous materials are subject to stringent safety laws. The main regulatory agency in charge of making sure that these compounds are handled safely in order to avoid mishaps and protect the environment and public health is the PESO. Following a number of required permits, rules, and procedures is what PESO compliance means. The required licenses and stakeholder requirements for PESO compliance, along with the ramifications for various industries, will be described in this article.
What is PESO and Why is It Essential?
The Petroleum and Explosives Safety Organization (PESO), established under the Department for the Promotion of Industry and Internal Trade (DPIIT), is tasked with enforcing safety regulations for hazardous substances in India. PESO’s mission is to regulate and monitor the use of petroleum, explosives, and hazardous materials by issuing licenses, maintaining safety protocols, and conducting inspections to minimize accidents and ensure public safety.
Types of PESO Licenses and Permits
1. Petroleum License
Industries storing, handling, and transporting petroleum products must obtain a PESO Petroleum License. This license is crucial for companies involved in refining, storage, and distribution. Depending on the quantity and type of petroleum stored, companies must apply for different classes of licenses, including:
- Petroleum Class A: Pertains to highly volatile substances like gasoline.
- Petroleum Class B: Covers kerosene and similar substances.
- Petroleum Class C: Includes fuel oils that have a higher flashpoint.
Obtaining a petroleum license requires submitting documents such as site plans, safety protocols, and compliance certificates to PESO for verification.
2. Explosives License
The Explosives License is essential for industries that manufacture, store, and transport explosives. This includes companies in the mining, fireworks, and defense sectors. The types of licenses under this category are:
- Manufacturing License: For facilities manufacturing explosives.
- Storage License: For entities storing explosives, often in bulk.
- Transportation License: For companies handling the transport of explosive materials.
Each license requires extensive documentation, including the premises’ structural layout, safety equipment, and emergency response protocols.
3. Compressed Gas License
Handling and storing compressed gases, such as liquefied petroleum gas (LPG) or natural gas, demands a specific PESO Compressed Gas License. This license is mandatory for LPG bottling plants, gas storage facilities, and industries using compressed gases in their operations.
The licensing process involves:
- Submitting safety plans and equipment details.
- Meeting technical requirements for gas handling.
- Conducting site inspections and safety audits.
4. Pressure Vessels License
The Pressure Vessels License is needed for industries operating pressure vessels or equipment containing gases and liquids under high pressure. This license ensures that facilities maintain structural integrity, proper maintenance, and safety protocols for pressure vessel equipment. Pressure vessel compliance involves regular inspections, certifications from licensed engineers, and adherence to PESO safety standards.
Stakeholder Requirements in PESO Compliance
PESO compliance demands adherence not only from the primary operator but also from associated stakeholders such as contractors, employees, equipment suppliers, and transporters. Understanding these stakeholder requirements is essential for a comprehensive PESO compliance framework.
1. Responsibilities of Employers and Facility Operators
Operators and employers are required to:
- Implement robust safety protocols for handling hazardous substances.
- Train employees on emergency response procedures and safety equipment usage.
- Ensure regular maintenance and safety inspections of storage and handling facilities.
2. Training and Awareness Programs for Employees
Employees play a critical role in ensuring PESO compliance. Training programs are required for employees handling hazardous substances. Key areas of training include:
- Safe handling and storage practices for petroleum and explosive materials.
- Risk management protocols to mitigate accidents.
- First aid and emergency response in case of accidental spills or explosions.
3. Contractor and Vendor Compliance
Contractors and vendors associated with PESO-compliant industries must adhere to safety standards set forth by PESO. They must undergo safety assessments, conduct inspections on equipment, and follow transportation guidelines for hazardous materials. Additionally, contractors should have access to approved safety gear and training.
The PESO Licensing Process: Steps to Ensure Compliance
Step 1: Application Submission
To obtain a PESO license, organizations must submit an application outlining their facility’s safety plans, structural blueprints, and handling protocols. The application must include details of the facility’s layout, storage capacities, and types of materials handled.
Step 2: Site Inspection by PESO Authorities
Once the application is submitted, PESO officials conduct an inspection of the premises to evaluate safety standards and structural compliance. They review aspects such as:
- Storage facility integrity and fire prevention systems.
- Adequacy of emergency exits and safety equipment.
- Ventilation systems for handling volatile substances.
Step 3: Documentation and Verification
Applicants must submit detailed documentation, including:
- Safety management plans and risk assessment reports.
- Structural blueprints and environmental impact assessments.
- Employee training records and maintenance logs.
PESO authorities verify this documentation to ensure all regulatory standards are met.
Step 4: Issuance of License and Renewal Requirements
Once the facility passes inspection and documentation is approved, PESO issues the relevant license. However, the license is valid for a specific duration and must be renewed periodically. Renewal involves re-inspection and updated documentation to ensure ongoing compliance.
Consequences of Non-Compliance with PESO Regulations
Non-compliance with PESO regulations can have severe repercussions, including penalties, suspension of operations, and even legal action. Companies failing to meet PESO standards may face:
- Fines for non-compliance.
- Operational shutdowns until compliance is achieved.
- Legal liabilities for accidents resulting from negligence.
Compliance ensures operational continuity and minimizes risks to personnel, the public, and the environment.
Conclusion
In India, PESO compliance is non-negotiable for industries handling hazardous materials, petroleum, explosives, and gases. Ensuring that all mandatory licenses are obtained and stakeholder responsibilities are fulfilled is essential to meet PESO’s stringent safety standards. Companies must prioritize safety protocols, regular employee training, and periodic equipment inspections to maintain PESO compliance.